Laminated Veneer Lumber (LVL) is an engineered wood product made from thin layers of wood veneer that are bonded together using adhesive. This innovative material is designed for structural applications, providing high strength and stability. LVL has become increasingly popular in construction due to its ability to outperform conventional lumber in various aspects.
At WoodenAve, we offer premium wood veneer solutions, including Laminated Veneer Lumber. In this article, we’ll tackle what is LVL lumber, what is laminated veneer lumber used for, and more.
Key Takeaways
- Laminated Veneer Lumber (LVL) is a high-strength engineered wood product made from layers of veneer.
- LVL is primarily used in structural applications such as beams, rafters, and I-joists.
- The manufacturing process involves bonding thin wood veneers with adhesives under pressure and heat.
- LVL offers great dimensional stability and resistance to warping compared to conventional lumber.
What is Laminated Veneer Lumber?
Laminated Veneer Lumber (LVL) is a type of engineered wood that consists of multiple layers of thin wood veneers bonded together with adhesives. The laminate veneers are typically rotary peeled or sliced from logs and can vary in thickness, often ranging from 2.5 to 4.8 mm. This method allows LVL to use smaller trees and reduce waste, making it a sustainable option in the timber industry.
LVL is known for its exceptional mechanical properties, which include high strength and dimensional stability. Unlike conventional lumber, which can warp or twist over time, LVL maintains its shape even under heavy loads. This makes it one of the most durable wood-based construction materials available today.
How is Laminated Veneer Lumber Made?
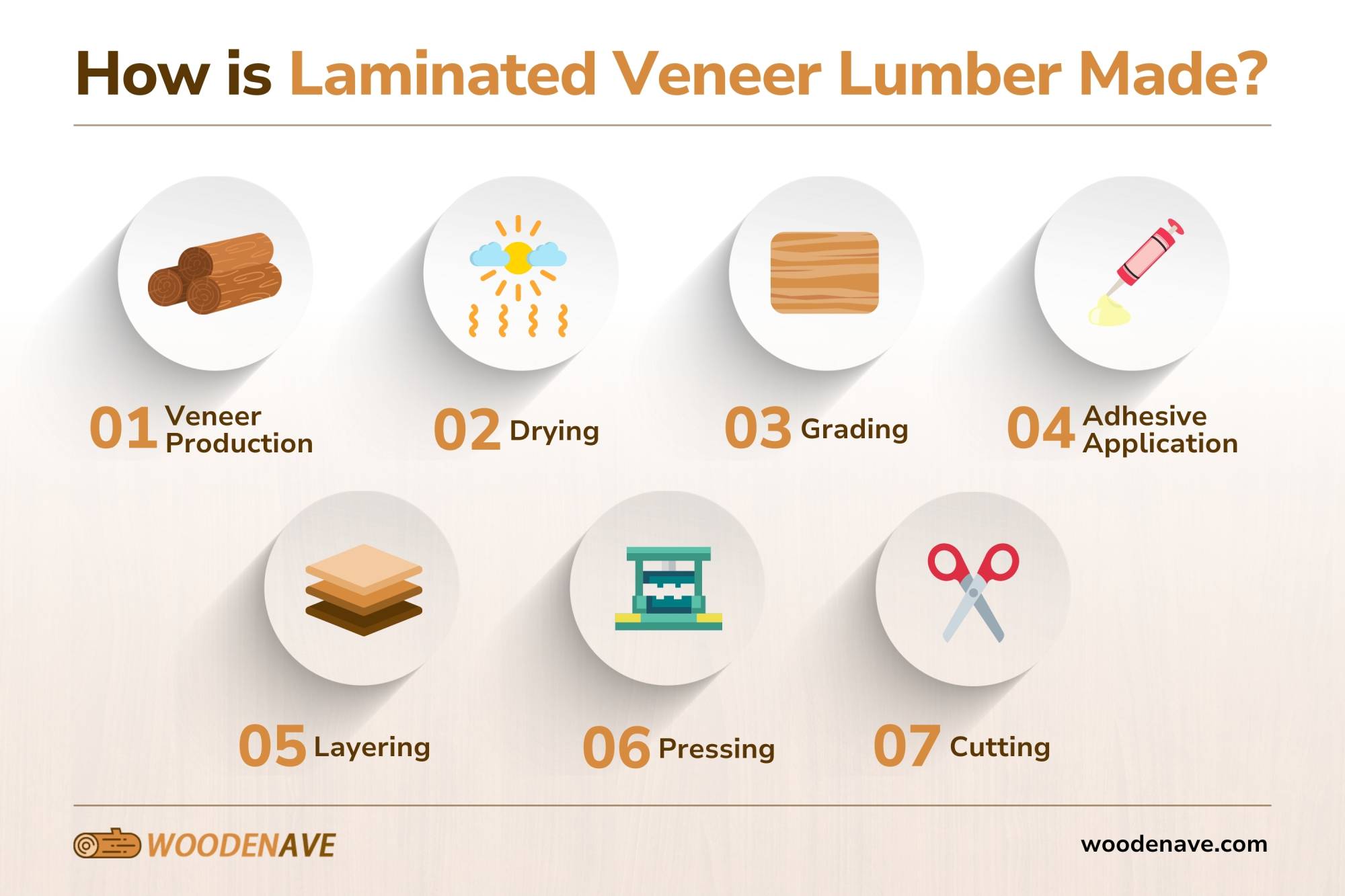
The manufacturing process of laminated veneer lumber involves several important steps, including veneer production, drying, grading, adhesive application, layering, pressing, and cutting:
- Veneer Production: Logs are processed into thin sheets of veneer using rotary peeling or slicing methods. The thickness of the veneer is crucial for the final product’s performance.
- Drying: The veneers are dried to a specific moisture content to prevent defects, including warping or mold growth.
- Grading: Dried veneers are graded based on their quality and natural defects. Higher-quality veneers are selected for structural applications.
- Adhesive Application: A strong adhesive, commonly phenol formaldehyde, is applied to the surface of the veneer. This adhesive provides excellent bonding strength.
- Layering: The veneers are stacked in layers with their grain arranged in a matching direction. This alignment enhances the overall strength of the LVL.
- Pressing: The layered veneers are then secured together under heat and pressure in a hydraulic press. This process ensures a strong bond between the layers.
- Cutting: Once cured, the LVL billets are cut into desired dimensions for various applications.
With careful control during each step in the LVL production process, a consistent and reliable engineered wood product that meets strict performance standards is created.
What is Laminated Veneer Lumber Used for?
Laminated veneer lumber is mainly used in structural applications due to its high strength and stability. According to research published by the Oklahoma State University Extension, laminated veneer lumber is one of the most popular engineered wood products for construction applications. Common uses include:
- Beams: LVL beams are often used as load-bearing members in residential and commercial buildings.
- Rafters: They provide support for roofs and help distribute loads evenly.
- I-Joists: LVL can be used to manufacture I-joists, which are essential components in floor framing systems.
- Headers and Lintels: LVL can serve as strong headers above doorways and windows.
- Custom Applications: Due to its versatility, LVL can also be used in specialized applications such as curved structures or unique architectural designs.
Overall, laminated veneer lumber is a great choice for constructions where strength and reliability are paramount.
The Benefits of LVL
Benefit | Description |
---|---|
High Strength | Engineered for superior strength, ideal for beams, rafters, and I-joists |
Dimensional Stability | Resists warping and twisting, ensuring consistent performance |
Sustainability | Uses fast-growing species and recycled materials, minimizing waste |
Versatility | Customizable sizes and shapes; compatible with other engineered wood products like LSL and PSL |
Predictable Performance | Consistent quality without natural defects, ensuring reliable structural performance |
Moisture Resistance | Adhesive bonding reduces moisture risks; proper sealing enhances durability |
Cost-Effective | Higher initial cost offset by durability, low maintenance, and faster assembly |
Product Compatibility | Integrates with products like glulam and plywood for optimized composite systems |
Laminated Veneer Lumber (LVL) provides a range of benefits that make it a fantastic choice for construction projects. These include high strength and load-bearing capacity, dimensional stability, sustainability, flexible design, predictable performance, resistance to moisture, cost-effectiveness, and compatibility with other wood products. Here are the main advantages of using LVL:
High Strength and Load-Bearing Capacity
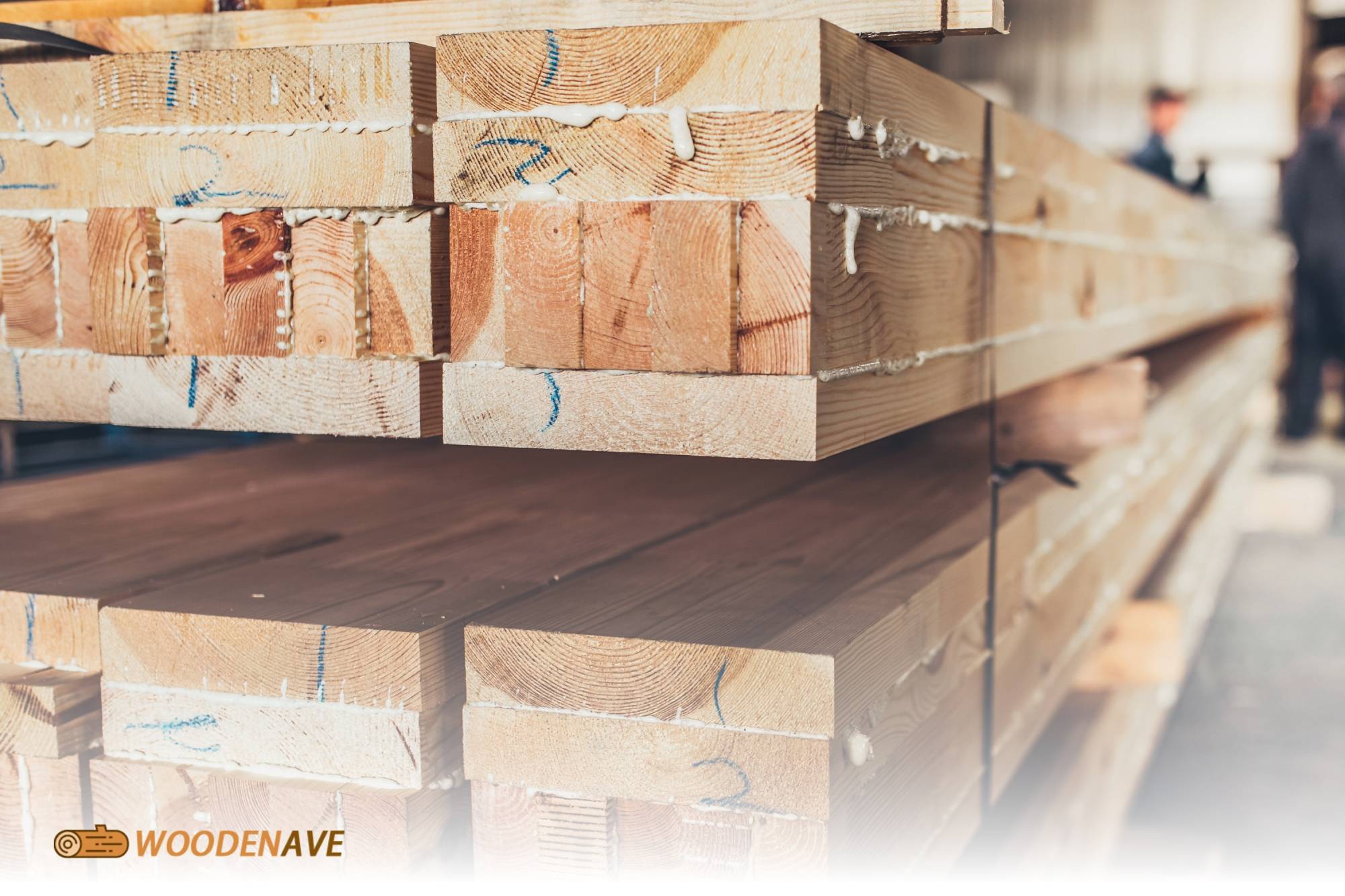
A case of LVL is engineered to deliver great strength, making it suitable for load-bearing applications. Its construction involves bonding multiple layers of thin wood veneers, which enhances its load-bearing capacity compared to conventional sawn lumber. This high strength allows LVL to be used effectively as forest products in beams, rafters, and I-joists, making it a reliable option in structural composite lumber applications.
Dimensional Stability
One of the standout features of LVL is its dimensional stability. Unlike traditional solid wood, which can warp or twist due to changes in moisture content, LVL is less prone to these issues. The lamination process helps stabilize the wood, ensuring that it maintains its shape for an extended time. This stability is essential in construction, where consistent performance is required.
Sustainability
LVL contributes to sustainable building practices by using fast-growing species of wood and minimizing waste during production. The manufacturing process allows for efficient use of wood resources, as smaller trees can be used to produce high-quality lumber. Additionally, LVL may be made from recycled materials, further enhancing its eco-friendly profile. By choosing LVL, builders can reduce their environmental footprint while still achieving high-performance results.
Versatility in Design
LVL’s versatility allows it to be used in a wide range of applications beyond traditional framing. It can be manufactured in various sizes and shapes, accommodating unique architectural designs and specifications. Whether used as beams or in custom structural components, LVL can adapt to different project requirements. This flexibility also extends to its compatibility with other engineered wood products, such as laminated strand lumber (LSL) and parallel strand lumber (PSL).
Predictable Performance
The controlled manufacturing process of LVL ensures that each piece has consistent quality and performance characteristics. Unlike solid-sawn lumber, which may contain natural defects like knots or grain irregularities, LVL is made from dried and graded wood veneers that are bonded together under heat and pressure. This predictability allows engineers and builders to design structures with confidence, knowing that LVL will perform reliably under load.
Resistance to Moisture Penetration
LVL’s adhesive bonding process enhances its resistance to moisture penetration compared to conventional plywood or solid wood products. While it is essential to protect LVL from prolonged exposure to water during construction, its inherent properties help mitigate the risks associated with moisture-related damage. Proper sealing and finishing can further enhance its durability against environmental factors.
Cost-Effectiveness
Although the initial cost of LVL may be higher than traditional sawn lumber, its long-term benefits often justify the investment. The durability and low maintenance requirements of LVL lead to reduced repair and replacement costs over time. Additionally, the efficiency of using LVL in construction — allowing for quicker assembly and fewer errors — can result in overall cost savings on building projects.
Compatibility with Other Wood Products
LVL can be easily integrated with other engineered wood products, such as glue laminated timber (glulam) and structural plywood. This compatibility allows builders to create composite systems that enhance structural performance while optimizing material usage. In many cases, LVL serves as an ideal alternative or supplement to solid-sawn lumber in various applications. In addition to LVL, there are tons of other veneer products that will work well for your application, such as natural wood veneers and backed veneer.
WoodenAve: Premium Wood Veneer
Now that we’ve covered what are LVLs, you’ll know that laminated veneer lumber represents a huge advancement in engineered wood products, combining strength, stability, and sustainability. At WoodenAve, we offer premium wood veneer solutions that cater to various construction needs, including high-quality LVL products.
Explore our range of wood veneers today and discover how our engineered wood solutions can improve your building projects!
FAQs on What is Laminated Veneer Lumber?
What are the disadvantages of laminated veneer lumber?
LVL can be prone to moisture damage if not properly sealed, limiting its use in wet environments. Unlike oriented strand boards, LVL requires specialized manufacturing, which can increase its cost.
Is laminated veneer lumber better than solid wood?
LVL offers greater dimensional stability and consistent strength properties of LVL compared to natural, solid wood. However, solid wood like Douglas fir may be preferred for its natural aesthetics in certain applications.
Is LVL stronger than hardwood?
LVL often surpasses hardwood in strength due to the engineered structure as part of composite lumber products. However, some dense hardwoods like Douglas fir may match or exceed LVL in specific applications.
Back to Top: What is Laminated Veneer Lumber?